When it comes to mechanical engineering, selecting the right tools can make or break a project. For engineers, the challenges of choosing the appropriate installation tool for their specific applications are compounded by a wide array of options and functionalities.
Atlas installation tools stand out among these options, but understanding which model to use for which job is crucial. Let’s delve into tool selection, focusing on the distinctions between pull-to-pressure and pull-to-stroke tools, critical considerations for selection, and the advantages of choosing HTF as your master stocking distributor.
Understanding Pull-To-Pressure vs. Pull-To-Stroke Tools
Pull-To-Pressure Tools
Pull-to-pressure tools operate by exerting a specified amount of pressure to achieve proper installation. These tools are particularly useful in applications where the amount of force applied directly impacts the performance of the connection or assembly. They are ideal for critical applications involving high-stress environments or materials requiring precise installation pressures to ensure integrity and safety.
For example, pull-to-pressure tools can be essential for applications like fastening components that experience high loads or vibrations in the aerospace and automotive industries. The tool's ability to maintain consistent pressure helps ensure that each joint is reliable and durable.
Pull-To-Stroke Tools
On the other hand, pull-to-stroke tools focus on the physical distance traveled during installation rather than the pressure exerted. These tools are generally used when the primary requirement is to achieve a certain depth or stroke in the installation process. Applications may include situations where the fit is critical, but the pressure must not be finely tuned.
For instance, pull-to-stroke tools are commonly employed in assembly lines for fasteners or connectors. Their main goal is to ensure that components are seated correctly without requiring precise pressure measurements. Industries such as manufacturing and construction frequently leverage these tools to achieve consistent and repeatable results.
Comparison of Pull-To-Pressure and Pull-To-Stroke Tools
The main distinction between pull-to-pressure and pull-to-stroke tools lies in their operational focus. Pull-to-pressure tools are geared toward applications where pressure measurement is critical, while pull-to-stroke tools prioritize stroke length. This difference leads to varied functionality and suitability depending on the engineering context.
In short, selecting between these tools requires a careful evaluation of the specific requirements of the application at hand, including the type of materials being used and the environmental conditions of the installation.
Key Considerations for Tool Selection
When selecting an installation tool, several important factors should be taken into account:
- Material Compatibility: Different materials react differently under pressure and stress. For instance, softer materials may deform under excessive pressure, while materials may require more force to achieve a secure fit. Understanding the tool's compatibility with the material in use is essential.
- Installation Environment: The surrounding conditions can significantly affect tool performance. Factors such as temperature, humidity, and exposure to chemicals can influence the tool and the materials being worked with. It's vital to select an installation site that can withstand its specific conditions.
- Required Precision: Different applications necessitate different levels of precision. Pull-to-pressure tools may be needed for high-precision tasks, while pull-to-stroke tools may suffice for general applications. Evaluating the precision required for the project will guide the selection process.
A common misconception is that one type of tool can cover all applications. In reality, a tailored approach frequently yields better results. Understanding the nuances of each tool type is crucial to avoid inefficiencies or failures in installations.
Atlas Series Installation Tools
HTF offers a range of Atlas installation tools tailored for both pull-to-pressure and pull-to-stroke applications. Some notable models include:
- Atlas PTP Series: These pull-to-pressure tools feature advanced pressure gauges and ergonomic designs, making them user-friendly and highly effective for applications where precision is paramount.
- Atlas PTS Series: Designed for pull-to-stroke installations, these tools provide adjustable stroke lengths, allowing engineers to customize their settings based on specific requirements.
Each tool has innovative features that enhance usability and ensure reliability across various engineering applications. Their design considerations, including weight distribution and handle ergonomics, promote ease of use, which is essential for long working hours on complex projects.
HTF: Your Source for Atlas Tools
When sourcing Atlas installation tools, HTF has a deep inventory of tools and guarantees timely supply to keep your projects on track.
HTF's service is evident in its team of experts ready to assist with tailored advice. For added convenience, HTF offers same-day shipping for orders placed by 3 p.m. Eastern, ensuring you receive your tools when needed.
In conclusion, choosing the right installation tool is crucial for successful mechanical engineering applications. By understanding the differences between pull-to-pressure and pull-to-stroke tools, considering key selection factors, and partnering with HTF for your Atlas tools, you can enhance the efficiency and reliability of your projects. Explore HTF’s offerings or HTF's Atlas expert today to find the best solutions for your needs. Reach out to HTF today; we’re here to help!
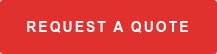