HTF is excited to spotlight our partner DTi (Device Technologies, Inc.). In 1984, Device Technologies, Inc. began in a farmhouse basement, later moving to a New England barn, and now operates from a 20,000-square-foot, climate-controlled facility. Their first major success was supplying Digital Equipment Corporation (now HP) with a UL94 V-0 Spring-Fast® Wire Protection Grommet Edging for the VAX Mainframe computer, resulting in substantial cost savings and a boost in productivity.
Since then, DTi has expanded its high-performance wire protection grommet line known for withstanding harsh conditions. It has earned a global preferred vendor status with industry partners. Their "Designed 2 Protect" solutions have led to the development of advanced equipment protection solutions incorporating fiber management, enclosure seals, thermal management, EMI shielding, and braided sleeving.
Through years of expertise, DTi continues its legacy of problem-solving, emphasizing a custom approach that prioritizes operational efficiency and high quality. Read on to learn more about grommet edging and how to pick the right solution for any project.
The Role of Grommet Edging
A grommet refers to a circular or eye-shaped insert placed into a hole to offer protective reinforcement along the exposed, uneven edges of the hole within a thin material. Grommets serve a dual purpose: they shield the material around the hole and enhance its structural integrity. Typically, grommets have two flared edges, ensuring a secure fit without requiring adhesives or fasteners. Their primary functions include reinforcing the material they are inserted into and safeguarding wires passing through the opening.
The grommet edging is crucial in shielding wires and cables from abrasion as they traverse sharp or rough surfaces. This safeguard is essential to prevent the deterioration of the cable's protective covering. Damage to wires and cables can lead to electronic and communication equipment failures or, in more severe cases, pose health and safety risks.
During the manufacturing of products, rough edges or burrs occur at the points where access holes are cut. This necessitates the application of grommet edging, also known as trim, directly onto the surface material to safeguard components like wires from potential harm. Grommet strips, a type of edging, can be custom-made to specific lengths and pre-cut for convenient installation in a chosen material.
3 Questions for Selecting Grommet Edging
What grommet edging material do I need?
Grommet edge protection comes in several materials. All DTi grommet materials meet specified standards for abrasion protection:
- Silicone rubber provides longevity and reduces the need for adhesive.
- Polyethylene is a durable thermoplastic with low friction.
- PVC, or polyvinyl chloride, is a synthetic thermoplastic that is naturally rigid. To make PVC work as a workable grommet edging, plasticizers must be added to make its flexibility consistent with the metal core. Combining the PVC with an aluminum core provides the ideal retention for installation without adhesives. Due to its strength and affordability, PVC is a cost-effective alternative for silicone rubber grommets.
- Nylon is also cost-effective for grommet edging. It is another synthetic thermoplastic used for grommet edging protection. It is strong and resistant to corrosion, chemicals, and abrasion. Nylon also a low surface friction, which will protect the cables from breaking down over time.
- Encapsulated metal strips are a strong choice for wire protection, sealing them off from environmental or thermal wear. DTi's have stainless steel substrate encapsulated with nylon or EPOXY, which provides strong edge retention. This lowers the installation cost and is more durable than grommets requiring adhesive. This merges the incredible performance of a metal substrate in harsh conditions with the extra protection of low friction nylon.
Choosing a grommet material depends also on its application.
What applicational conditions will the grommet be exposed to?
The intended function of the grommet plays a pivotal role in determining its overall design. A desk grommet, for instance, typically features an open design and is constructed from plastic or rubber to shield phone and computer cables from potential damage caused by contact with rough wood or metal edges.
Additionally, there are grommets with soft materials that can be customized to accommodate wire passage while preventing debris or dust from entering, all while securely guiding and holding the cable in its desired position.
What type of installation method is required?
There are several installation and attachment methods for grommet edging. DTi's use simple snap-on installations like the Spring-Fast, as well as the snap-on fusion attachment method of the Spring-Fast Aerospace Grommet.
Installation type is dependent on industrial application, as aerospace or military grommet edging may be exposed to specific environmental extremes. Aerospace products are sealed with a bonded EPOXY, for example. Still, all of DTi's edging is snap-on, which greatly simplifies the process of adding grommet edging.
The DTi Advantage
How frequently can you cut the cost of a component in half? DTi’s grommet edging snap-on installation method reduces costs by a significant 49% compared to grommets that require glue. This streamlined process enhances efficiency by a remarkable 9.5 times, reducing workflow complexity.
Ultimately, DTi's Spring-Fast Grommet Edging is a cost-effective solution that enhances wire and cable protection, reduces installation complexities, and offers a wide range of applications. Their commitment to innovation and customer satisfaction continues to drive their success.
Our experts at HTF are here to help you select the proper grommets for your needs. Reach out for a quote, and make HTF your first choice today!
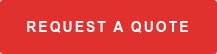